Enhancing Safety and Efficiency: The Importance of Welding Curtains
In the world of welding, safety is paramount. Welding operations involve intense heat, bright arcs, and hazardous particles that can cause severe injuries if proper precautions are not taken. Among the many safety measures available, welding curtains play a crucial role in safeguarding both welders and their surrounding environment. These specialized curtains are designed to provide a protective barrier that ensures the safety of personnel and helps optimize welding efficiency. In this post, we will explore the importance of welding curtains and their significant benefits in welding environments.
Safety and Eye Protection: Welding curtains primarily serve as a protective barrier against harmful welding arcs, sparks, and flashes. These curtains are made from durable materials, such as flame-retardant vinyl, that effectively block UV radiation and infrared light generated during welding processes. By preventing exposure to these hazardous elements, welding curtains safeguard the eyesight of both welders and other workers in the vicinity.
Containment of Hazards: Welding curtains create a defined workspace by isolating the welding area from the surrounding environment. This containment helps prevent the spread of harmful fumes, sparks, and debris, reducing the risk of accidents and injuries. By confining the welding zone, curtains help maintain a safer working environment and protect nearby workers from potential hazards.
Enhanced Efficiency and Productivity: In addition to ensuring safety, welding curtains contribute to increased productivity and efficiency. By creating a controlled work area, curtains help minimize distractions, allowing welders to focus on their tasks. The clear visibility provided by the curtains enables welders to monitor their work closely, resulting in improved accuracy and quality of welds. Moreover, the contained space reduces the need for extensive cleanup after welding, saving time and effort.
Versatility and Customization: Welding curtains come in various sizes, styles, and colors to suit different welding environments. Whether it’s a small welding booth or a large industrial facility, curtains can be customized to fit the required dimensions. Additionally, they can be equipped with features like transparent viewing panels, sliding strips, or even noise-reducing properties. This versatility allows for tailored solutions that cater to specific welding needs, ensuring maximum effectiveness and usability.
Flexibility and Portability: Another advantage of welding curtains is their flexibility and portability. They can be easily installed, repositioned, or removed as per the changing needs of a welding operation. This flexibility allows welders to adapt their workspaces to accommodate varying projects, layouts, or equipment. Portable welding curtains are particularly useful for temporary or mobile welding setups, providing a quick and convenient safety solution.
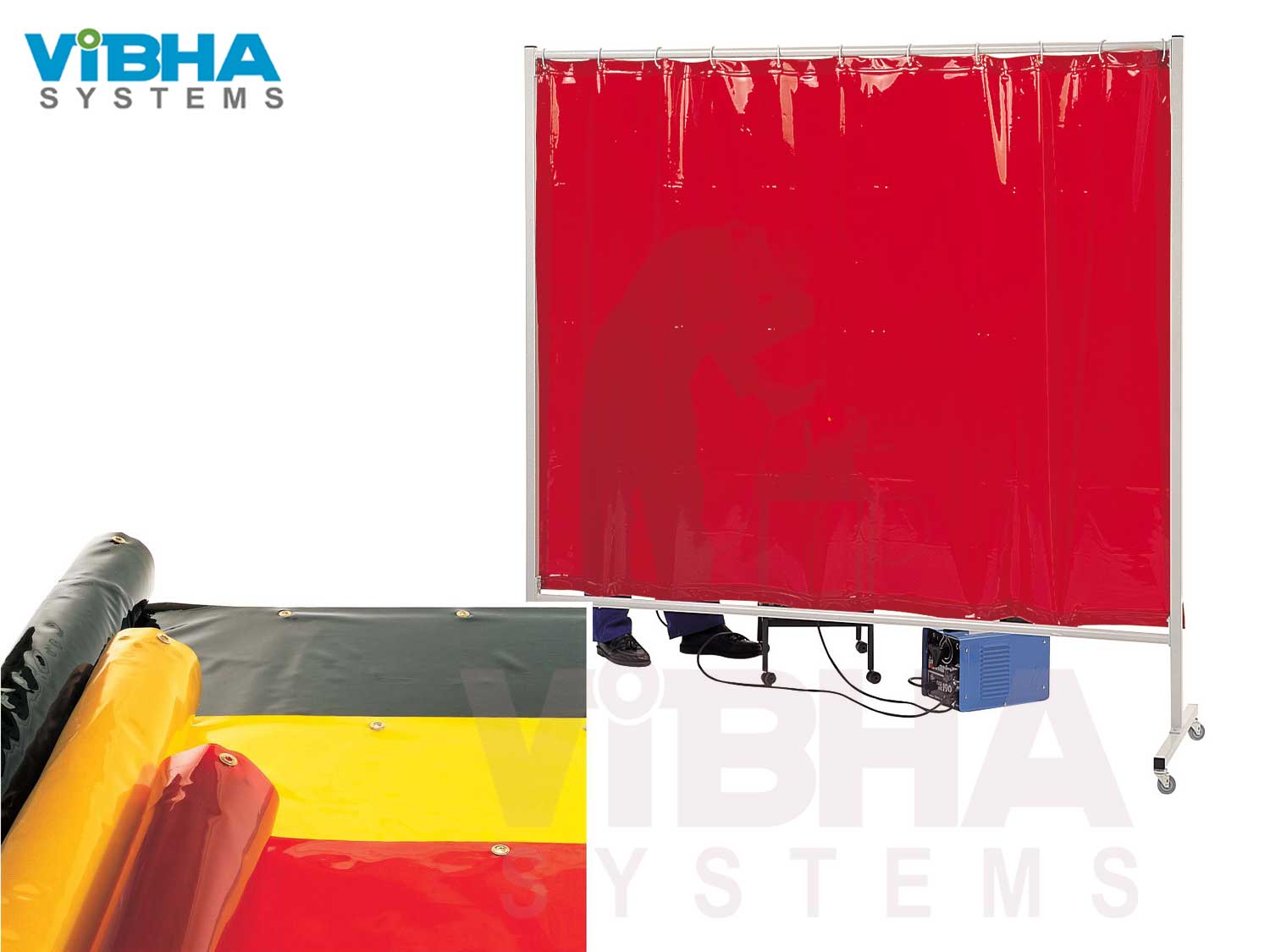
Metal fabrication areas involve various welding processes that require utmost safety precautions. In these environments, welding curtains serve as indispensable tools for protecting personnel, equipment, and surrounding areas. By understanding the advantages of welding curtains, metal fabrication facilities can create a safer and more efficient working environment. In this post, we will explore the specific benefits of welding curtains in metal fabrication areas.
Protection from Harmful Welding Hazards: Welding curtains act as a barrier against hazardous elements generated during welding, such as intense UV radiation, bright arcs, sparks, and hot metal particles. By effectively blocking these dangers, welding curtains safeguard the eyes, skin, and respiratory systems of workers in the metal fabrication area. This protection reduces the risk of welders suffering from eye injuries, burns, or respiratory issues caused by prolonged exposure to welding hazards.
Containment of Welding Fumes and Debris: Welding processes produce fumes, smoke, and debris that can be harmful if inhaled or accumulate in the surrounding area. Welding curtains create a controlled workspace by confining these byproducts within the designated welding zone. By containing fumes and debris, the curtains prevent their dispersion, minimizing the health risks for workers in the metal fabrication area. This containment also ensures that nearby equipment and materials are not contaminated or damaged by welding residues.
Enhanced Safety for Nearby Workers: Metal fabrication areas often involve multiple workstations or adjacent work areas. Welding curtains provide a vital safety measure by creating a clear separation between the welding operation and other workers in the vicinity. By isolating the welding zone, curtains prevent accidental contact with welding sparks, arcs, or molten metal, minimizing the risk of injuries to nearby personnel. This increased safety enables other workers to continue their tasks without fear of exposure to welding hazards.
Optimal Visibility and Improved Workflow: Welding curtains are available in various styles, including transparent viewing panels or tinted screens, which allow welders to maintain visibility while working. This clear visibility ensures that welders can closely monitor their welding processes, resulting in improved accuracy and weld quality. Additionally, welding curtains reduce distractions from surrounding activities, helping welders maintain focus and concentration. The controlled and visually unobstructed workspace provided by the curtains promotes an efficient workflow, enhancing productivity in metal fabrication areas.
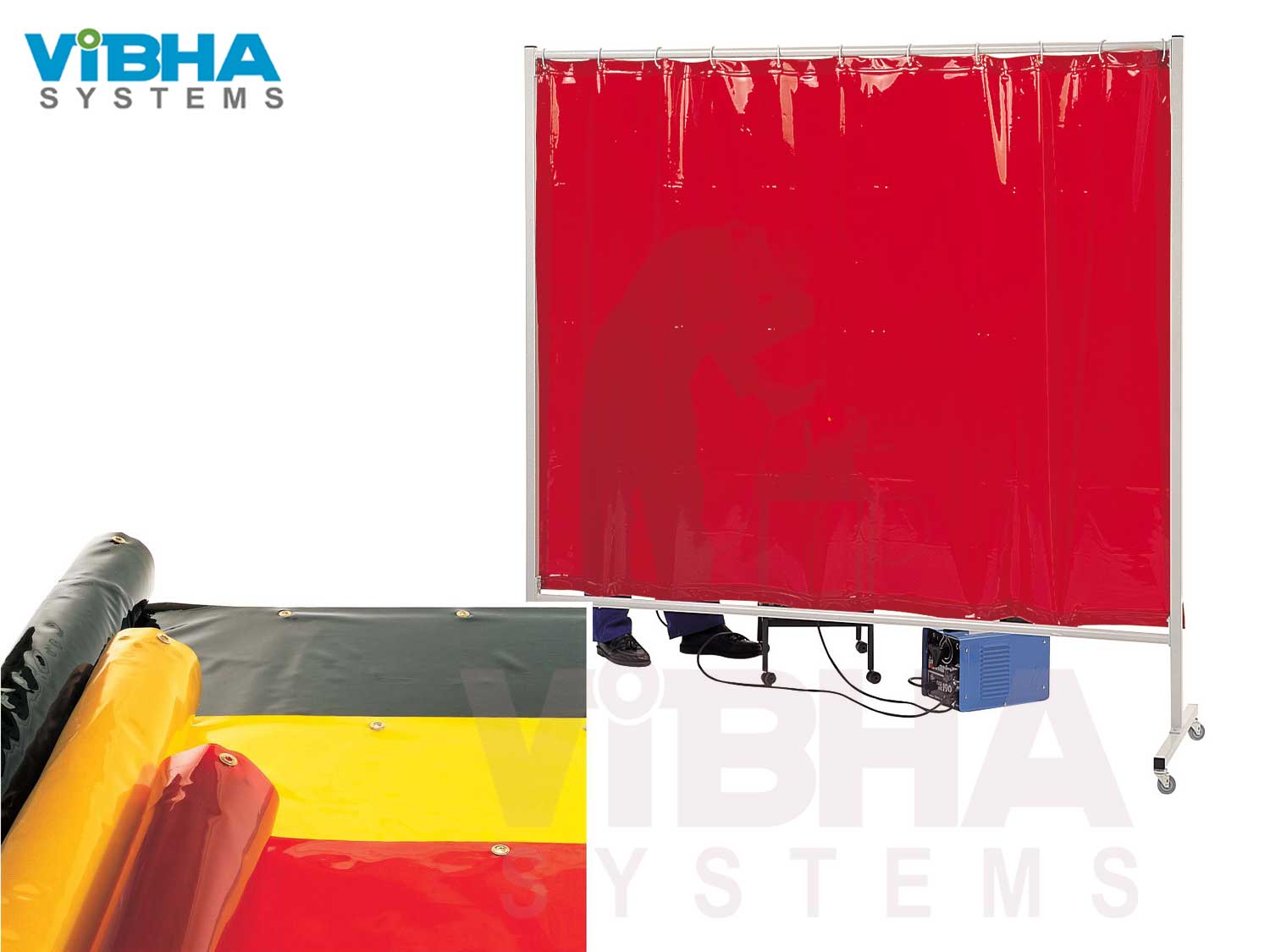
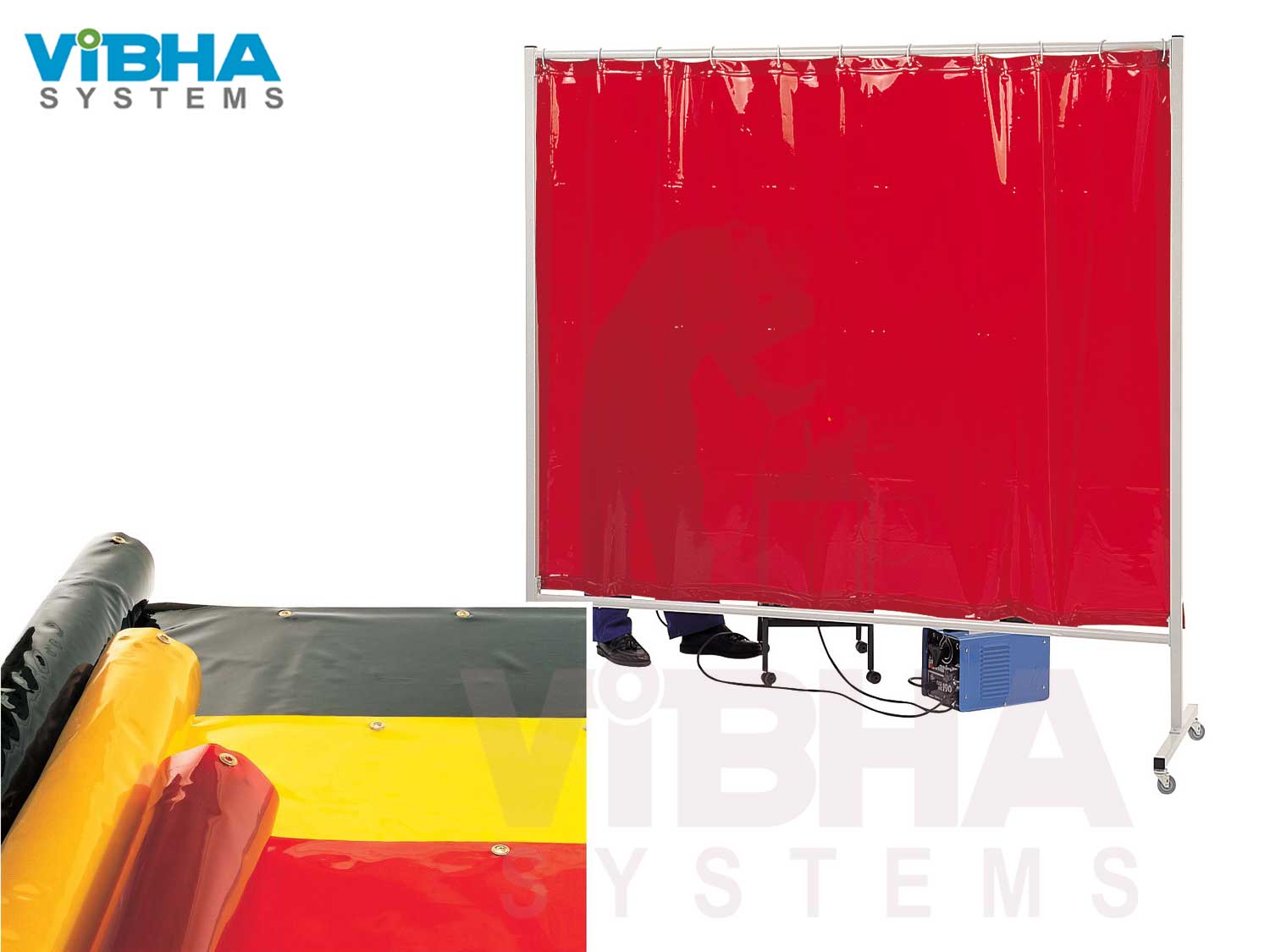
Customization and Flexibility: Welding curtains can be customized to suit the specific needs of a metal fabrication area. They are available in different sizes, lengths, and configurations, allowing for the creation of tailored solutions. Whether it’s a small welding booth or a large fabrication facility, curtains can be adapted to fit the required dimensions. Moreover, curtains with features like sliding strips or noise-reducing properties can be incorporated based on the unique requirements of the environment. This customization and flexibility ensure that welding curtains seamlessly integrate into the metal fabrication area, optimizing their effectiveness.